Catalyst Reactor Diagnosis Optimise refinery performance
Check your trickle flow reactor for signs of maldistribution
Refinery processes such as hydrotreating and hydrocracking use fixed bed trickle flow reactors. In these catalyst reactors the liquid (feedstock &
products) trickle down over the fixed bed of catalyst.With good reactor internals and a properly loaded catalyst bed, the velocity of the liquid in
the reactor will be homogeneous across the cross section of the reactor and along the length of the catalyst bed.Such uniform velocities are a pre-condition
for optimal catalyst performance, high conversion and long catalyst life.Unfortunately, maldistribution can occur.Depending on the degree of maldistribution
the consequence for the refinery margin may be more or less severe.In all cases it is necessary to check the maldistribution from time to time (preferably
monthly) to check the condition of the unit, to detect possible causes of maldistribution related to operating conditions, or to prepare for corrective
actions during the catalyst change-out. We find that many refineries struggle with determining the liquid velocities in their trickle flow reactor
causing inadequate monitoring, non-optimal performance of the unit, and surprises during change-outs.That’s why Catalyst Intelligence has developed
a new tool to analyse the velocities without interfering in the operating conditions of the reactor.We can analyse your detailed unit data off-line
and issue a report on the condition of the unit with respect to maldistribution.
We offer this service for free for first-time users in 2019.
Causes of maldistribution in catalyst reactor
Maldistribution in a trickle flow catalyst reactor may occur as a consequences of a number of causes.Sometimes the maldistribution is evident right
from the start of the cycle, and in those cases it may be caused by improper loading or poor catalyst quality resulting in different bed densities
in different places in the reactor causing preferential flow through parts of the bed with highest void fraction and least flow restriction. It
may also be caused by improper reactor internals or incorrect installation of the internals (non-horizontal), or the omission of seals between
the internals and the reactor wall allowing for gas and liquid to by-pass the distribution tray.
However, it is also possible that maldistribution develops over the cycle of the unit. This can be caused by settling of the bed in case it was sock
loaded, pressure shocks through the bed causing the bed to compact, fines entering the reactor, or coke built up in certain spots in the bed, catalyst
agglomeration, fouling of reactor outlet stool, failing or fouling of reactor internals during the cycle, to mention just a few potential causes.
When such a deviation starts to occur it is important to detect it early and consider what is going on, and what may be done to achieve optimum
catalyst performance during the rest of the cycle.Thus, many refineries try to measure maldistribution as part of their unit monitoring.In case
performance of the unit is deteriorating it is easy to detect.The drop in performance (or deviation from optimum) may be caused by maldistribution
and if that is the case, it is important to understand the extent of the maldistribution and decide on possible corrective measures.
Diagnosis of maldistribution
Today, refineries are checking maldistribution in trickle flow reactors by giving a temperature pulse to the feed and checking the response of
thermo-couples at different locations in the catalyst bed(s).The disadvantage of this technique is that it up-sets normal operation and give
may rise to off-spec products, or aggravation of an already existing maldistribution actually making a situation worse by the diagnosis.To
alleviate these drawbacks associated with today’s common practice, Catalyst Intelligence has developed a new proprietary technique to measure
flow-rates in a trickle flow reactor.The main advantage of this method is that the refiner does not need to produce a temperature pulse through
the catalyst bed.In fact we base our analysis on a detailed review of normal operating data and frequent temperature read-outs.By looking at
the detailed data we can determine flow-rates in certain parts of the reactor and compare to other parts of the reactor.The method is based
on read-outs of the thermo-couples , so the resolution in the reactor still depends on the number and location of the thermo-couples inside
the catalyst bed.
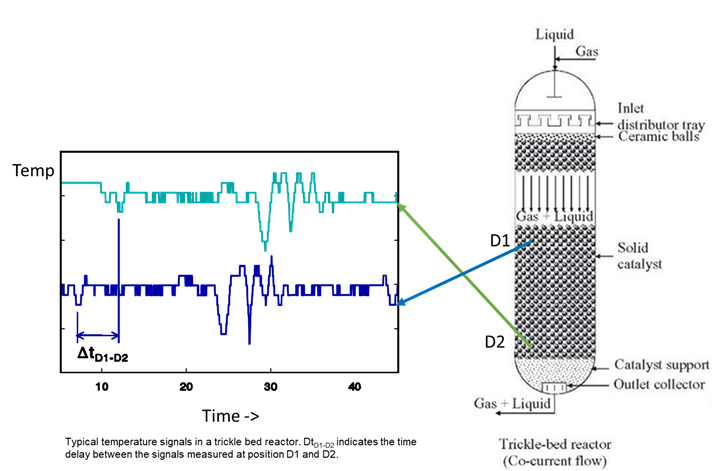
Corrective actions on maldistribution
Depending on the findings of the maldistribution we need to establish a likely cause of the maldistribution. This will usually involve a review
of other data and reports such as a loading diagram, catalyst certificates of analysis, a reactor installation report with photographs
and possibly videos, but can also entail operating data such as hydrogen flow rate, feed flow rate and feed quality. We need to look for
changes that may have caused the maldistribution to develop during the cycle and we need to decide which corrective actions need to be
undertaken to make sure performance remains acceptable.
In case the maldistribution is caused by improper installation of the catalyst reactor internals in the top of the reactor, a short stop and
correction may be sufficient to address the situation and such a correction may dramatically improve the performance. However, if the maldistribution
is caused by incorrect loading or poor catalyst quality a dump, screen and re-load may be necessary, or in case the catalyst quality is
really too bad a full replacement may be necessary.
Unique free offer
Catalyst Intelligence is willing to let each customer check our tool for free once.In case a refinery is interested to
have this analysis done on a regular basis we will propose a contract for a number of units and a certain period of time. Each analysis
requires the refinery to send us detailed temperature data and a description of the unit.We will perform the analysis and issue a report
with explanation of the observations.In case a refinery requires a more in depth analysis following our report, we are ready to assist
in any root cause analysis. As our staff has conducted such investigations many times during the course of their careers, we can help
you save valuable time and help you correct the problem before the issue shuts you down with significant impact on refinery margins.
Catalyst-Intelligence is a consulting company providing independent & comprehensive advice on fixed bed catalysts to refineries and
petrochemical plants.
If you are interested in using our free tool, please contact us.
For more information on how we can help you we refer to our website: www.catalyst-intelligence.com
-van der Grift Catalyst Specialist Jan 17, 2019